Cos’è la pressofusione
La pressofusione, altresì detta pressocolata o “fonderia in conchiglia sotto pressione”, è un processo che si è sviluppato negli Stati Uniti di metà ‘800 e che permette la realizzazione di stampi metallici in serie, dal basso costo, di rapida produzione e dall’elevata precisione.
Perché si dice “a conchiglia sotto pressione”?
Con il termine pressofusione si intende il processo produttivo di fonderia grazie al quale un metallo (con punto di fusione basso, come ad esempio zinco o alluminio) viene iniettato ad alta pressione in uno stampo metallico per creare prodotti in serie dalla forma desiderata e permanente.
La pressofusione è una tecnica di trasformazione dei metalli piuttosto recente, che consente la loro lavorazione in modo veloce e con alto grado di finitura.
L’elevata pressione pneumatica o idraulica forza il metallo fuso in uno stampo, solitamente in acciaio. L’ottima resistenza termica delle matrici in acciaio consente di poi produrre ripetutamente parti altamente complesse, anche con elevate tolleranze.
Nonostante in questo tipo di trasformazioni siano ugualmente impiegabili magnesio, zinco e alluminio, quest’ultimo rappresenta circa l’80% delle parti pressofuse.
Le sue caratteristiche permettono un veloce e preciso riempimento della cavità dello stampo e anche un’ottima finitura del pezzo pressofuso, con pochi difetti.
È importante, però, che la lega fusa mantegna sempre la temperatura ottimale durante tutto il processo di lavorazione, per evitare la formazione di soffiature.
Oggi la tecnologia risolve questa necessità con isole di produzione fornite di forni, completamente automatizzate e controllate da dispositivi di termoregolazione: computer in grado di intervenire in qualsiasi fase della produzione per regolare i parametri e assicurare la massima efficienza produttiva.
Ecco perché la pressofusione si presta ad un’elevata produttività e ad una ancora maggiore garanzia di tolleranze dimensionali minime e finiture superficiali di alta qualità e durabilità.
I suoi vantaggi sono molteplici, a partire da quelli intrinsechi alle caratteristiche della lega utilizzata: l’alluminio, per esempio, assicura leggerezza, resistenza alla corrosione, buona conducibilità termica ed elettrica, lavorabilità e soprattutto riciclabilità, che si sommano ai tanti vantaggi produttivi del processo di pressofusione.
Insomma, la pressofusione si mostra fruttuosa sia per il prodotto finale che per il processo produttivo in sé.

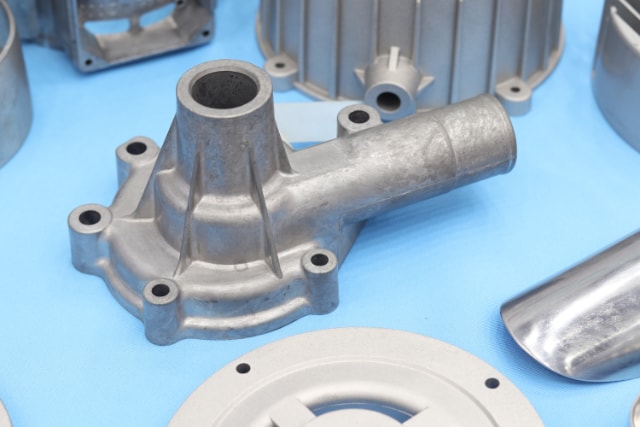

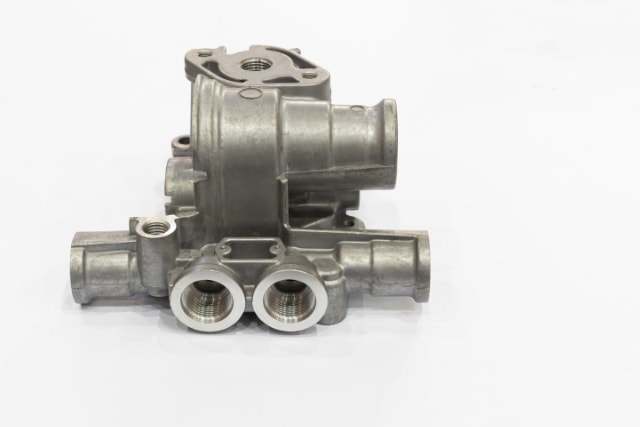
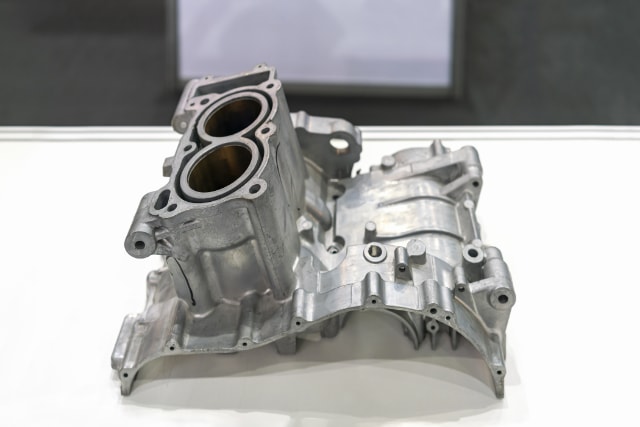
Fasi del processo di pressofusione dell’alluminio

1
Progettazione
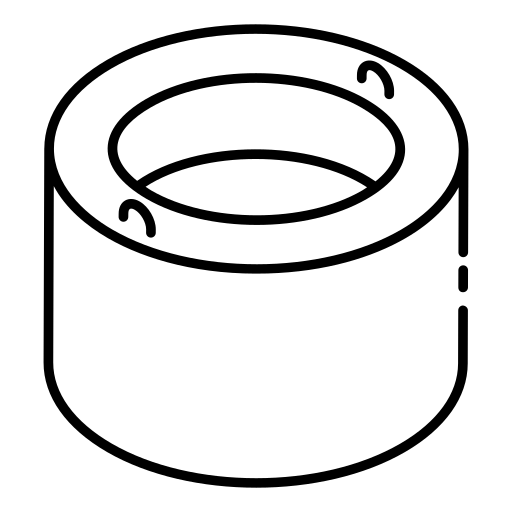
2
Stampo

3
Processo fusorio

4
Pressofusione

5
Finiture
La fase di progettazione preliminare permette, oltre alla preparazione dello stampo, di intervenire sui parametri di temperatura e pressione desiderati, per ottenere minori tempi di riempimento e alta qualità nel grado di finitura dei pezzi pressofusi.
Lo stampo è la cosiddetta “conchiglia”: possiede valori di temperatura di fusione maggiori rispetto all’alluminio, per resistere al calore a cui è sottoposto durante la fase di pressa.
Il processo fusorio è la fase concreta di fusione del metallo. È fondamentale che la temperatura del metallo rimanga costante anche nella fase successiva di iniezione e pressa.
La pressofusione è il processo centrale dell’intera trasformazione dell’alluminio. In questa fase l’alluminio viene iniettato e compresso ad elevate pressioni all’interno dello stampo.
Le finiture sono quei trattamenti finali che permettono al prodotto di raggiungere un particolare aspetto estetico e/o determinate caratteristiche metalliche.
Il processo di pressofusione dell’alluminio
Si calcola che la maggior parte dei prodotti metallici di tutti i processi di fusione sia realizzata mediante tecnica di pressofusione.
Per questa tipologia di produzioni, la pressofusione (definita anche con il termine “die casting”) è sicuramente la più indicata.
La combinazione di fusione e pressione permette di ottenere vantaggi che la sola fusione non garantirebbe tra cui:
- produzione in grandi volumi
- qualità
- velocità
- precisione
- ripetibilità
- versatilità
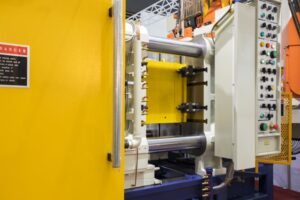

Progettazione
La pressocolata è un processo complesso che richiede attenzione a variabili cruciali come pressione e temperatura.
Nella fase di progettazione, queste due variabili emergono come i pilastri su cui si regge la qualità dei getti pressofusi e la produttività complessiva.
L’equilibrio tra pressione e temperatura gioca un ruolo fondamentale. Pressioni elevate facilitano il rapido riempimento degli stampi, aumentando la produttività, ma pressioni basse sono essenziali per evitare difetti causati dalla velocità d’ingresso del metallo fuso e per preservare la forma del pezzo. In particolare, pressioni elevate contribuiscono a prevenire la formazione di risacche di gas nel getto, riducendo il rischio di difetti nelle fasi successive del processo, come ad esempio soffiature.
La gestione della temperatura è altrettanto critica.
Un bilanciamento accurato è necessario: temperature troppo basse possono portare alla solidificazione prematura del getto o al mancato riempimento della forma, mentre temperature eccessivamente alte influiscono sui tempi di raffreddamento e, di conseguenza, sulla produttività complessiva.
Nonostante i valori di pressione e temperatura possano essere stimati durante la progettazione, la complessità del processo richiede spesso prove di stampa reali per stabilire empiricamente questi parametri.
Inoltre, l’adozione diffusa dei sistemi sottovuoto negli ultimi anni ha introdotto una nuova dimensione al processo, aumentando la pressione all’interno della forma e migliorando il riempimento dei pezzi, soprattutto quando la pressione rimane costante fino alla solidificazione.
La pressione, attentamente calibrata, tiene conto delle caratteristiche desiderate nel processo, garantendo tempi di riempimento ottimali e riducendo difetti, mentre la temperatura, gestita con precisione, assicura una fluidità adeguata evitando solidificazioni premature.
In alcuni casi, l’uso di sistemi sottovuoto aggiunge un livello di controllo supplementare, creando una differenza di pressione ulteriore nell’iniezione del liquido e facilitando il riempimento della forma.
In definitiva, la pressocolata è una danza intricata di pressione e temperatura, dove la maestria nell’equilibrare questi elementi determina la qualità del risultato finale e l’efficienza complessiva del processo.
Stampo
Le matrici impiegate nel processo di pressofusione, comunemente realizzate in acciaio o ghisa, sono composte da due semistampi che permettono l’estrazione del pezzo fuso dopo la formazione a stampo chiuso.
Le parti dello stampo sono realizzate con metalli ad alto punto di fusione, notevolmente superiore rispetto a quello delle leghe di alluminio, magnesio o zinco tipicamente iniettate durante il processo.
La pressione di iniezione del metallo fuso varia da 2 a 150 MPa e viene mantenuta costante fino alla fase di solidificazione grazie a presse idrauliche che assicurano la chiusura dello stampo.
Il raffreddamento del pezzo è garantito da un sistema di circolazione di liquido all’interno dello stampo. Una volta solidificato e raffreddato, il pezzo viene estratto aprendo i due stampi.
Rispetto alle forme tradizionali di fonderia in terra, la cavità del getto dello stampo per pressocolata può presentare spessori più sottili (fino a 1 mm), agevolati dall’alta pressione, ma deve evitare zone massive per garantire un raffreddamento uniforme del pezzo.
L’estrazione del pezzo dallo stampo è più complessa: è necessario l’uso di tasselli per affrontare eventuali sottosquadri. Il processo è progettato in modo che, al momento dell’estrazione, il pezzo sia solidale con la parte mobile dello stampo, agevolando così una rapida rimozione.
Fusione
La pressione di iniezione del materiale fuso può variare dai 2 ai 150 MPa a seconda del peso del pezzo da ottenere, ma anche della tipologia del materiale da fondere.
È importante che questa sia poi mantenuta costante per tutta la durata del processo, fino cioè alla solidificazione del pezzo, nella quale il pezzo pressofuso viene estratto dagli stampi.
Si possono distinguere due tipologie di lavorazione per pressofusione:
Pressofusione a caldo
Si definisce pressofusione a caldo se il serbatoio del metallo fuso è integrato in una fornace.
La presenza della fornace e le maggiori dimensioni del serbatoio, garantiscono un maggior controllo della temperatura di esercizio: il prelievo diretto dal serbatoio rende il processo più veloce, con una lega che risulta più uniforme come composizione e temperatura rispetto alla camera fredda, dunque una qualità di prodotto migliore.
Per contro la temperatura a caldo non può eccedere la soglia limite per non compromettere la produttività del processo, evitando lunghi tempi di raffreddamento.
L’utilizzo di questo processo è dunque limitato a metalli a basso punto di fusione, con una pressione di mantenimento più bassa rispetto alla camera fredda e corrispondente a valori compresi tra i 2 e i 15 MPa.
Pressofusione a freddo
La pressofusione si definisce a camera fredda se il serbatoio del metallo è una semplice cavità, a temperatura non controllata.
Il processo a camera fredda si caratterizza per una minore gestione della temperatura del metallo fuso e una produttività ridotta. Ciò è dovuto principalmente ai tempi più lunghi necessari per l’introduzione del metallo fuso e, soprattutto, alla temperatura di esercizio notevolmente superiore rispetto alla camera calda. Sebbene questo comporti una diminuzione della capacità produttiva, il processo compensa offrendo maggiore flessibilità nella selezione dei materiali adatti.
La pressione di mantenimento in questo contesto è notevolmente più elevata rispetto alla camera calda, variando tra 15 e 150 MPa.
Finiture
Come da lavorazione
I prodotti in zinco (dunque anche le leghe di zinco e alluminio) hanno una buona resistenza alla corrosione e possono essere impiegati anche senza finitura.
Di contro, trovandosi a che fare con magnesio e alluminio è consigliato un rivestimento resistente alla corrosione.
Un trattamento per anodizzazione deposita una finitura di ossido anodico sulla superficie dell’alluminio, rendendolo resistente alla corrosione. Le parti possono poi essere colorate in vari colori come nero, oro, trasparente e rosso.
Verniciatura in polvere
Durante il processo di verniciatura in polvere il prodotto viene spruzzato elettrostaticamente con vernice in polvere e successivamente riscaldato tramite un forno per il fissaggio della colorazione.
I vantaggi della pressofusione dell’alluminio
Abbiamo già avuto modo di introdurre i numerosi benefici che il processo di pressofusione permette di ottenere, tra i quali non possiamo non ricordare:
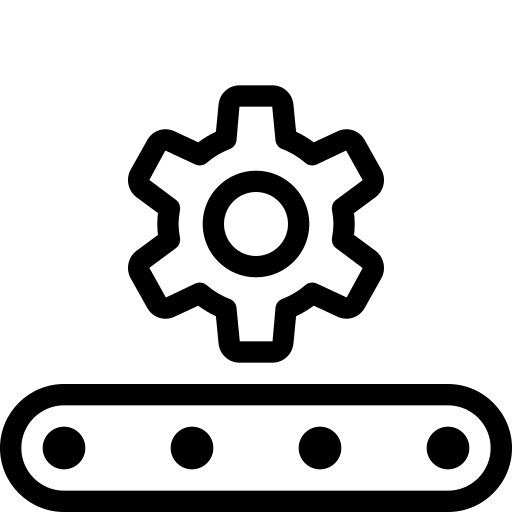
Produzione in serie
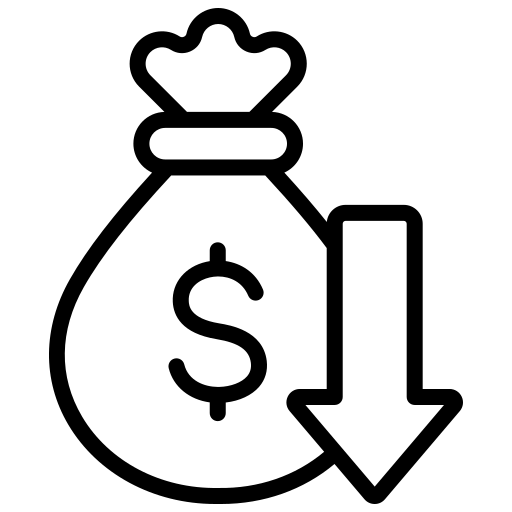
Riduzione dei costi
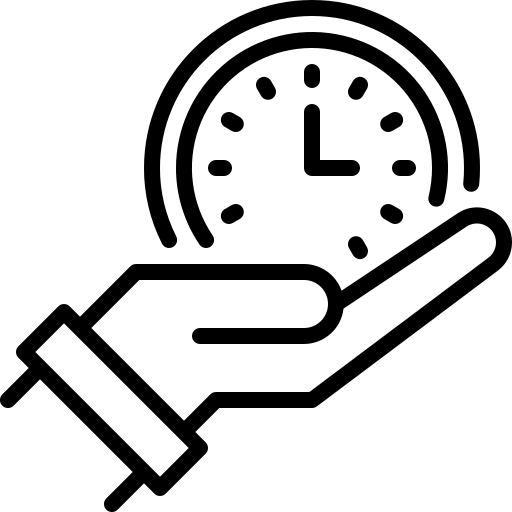
Riduzione del tempo
Ma non solo!
Vediamo insieme tutti i vantaggi che rendono questa lavorazione così competitiva:
- Produzione in serie con unico stampo
- Riduzione del tempo di produzione
- Riduzione dei costi di produzione
- Possibilità di ottenere forme complesse
- Alta qualità del prodotto pressofuso
- Riduzione delle impurità e dei difetti di produzione
- Precisione anche con tolleranze molto ridotte
- Precisione anche con spessori sottili
- Durabilità
- Buona resistenza a trazione
- Ottimo coefficiente di modulo elastico
- Altissima resistenza meccanica
- Ottima finitura superficiale
- Ottimo riscontro estetico
- Ampiezza di applicazioni in vari settori
- Ampiezza di leghe impiegabili
La pressofusione dell’alluminio è un processo produttivo relativamente recente, con un passato di “soli” duecento anni.
Se oggi riesce a garantire standard qualitativi così elevati è per l’evoluzione tecnologica a cui è andata incontro e che l’ha resa, oggi, la tecnologia più economica e performante per la produzione di oggetti in leghe di alluminio.